What are AGVs?
Automatic Guided Vehicles (AGVs) are driver-less, computer-controlled vehicles that move products and materials between locations in a warehouse, or within a manufacturing or distribution facility. These mobile robots reduce overhead by limiting the number of employees needed for material handling. They also increase efficiency by reducing damage to goods from accidents and worker injuries from bending, lifting, and fatigue. Typically, AGVs replace driver-operated trucks or forklifts that move pallets, boxes, or trays.
In warehouses like the ones used by the e-commerce giant Amazon, AGVs are part of larger automated storage and retrieval systems (AS/RS) with shuttles, cranes, carousels, vertical lift modules (VLMs), unit loads, mini loads, and micro loads. In these environments, AS/RS technology is usually integrated with warehouse management and warehouse execution software. The benefits of a robust AS/RS system are many, and include increased inventory storage density, order picking accuracy, and product security.
How do AGVs work?
AGVs navigate warehouses along either a fixed path or a free path. A fixed path relies upon magnetic navigation and, because the route is static, path changes are inconvenient. A free path uses laser positioning, visual positioning, millimeter wave radar (MMWR), inertial navigation, or global position system (GPS) technologies instead. AGVs that follow a fixed path may follow markers or wires in the floor. AGVs that follow a free path can leverage wireless communications instead.
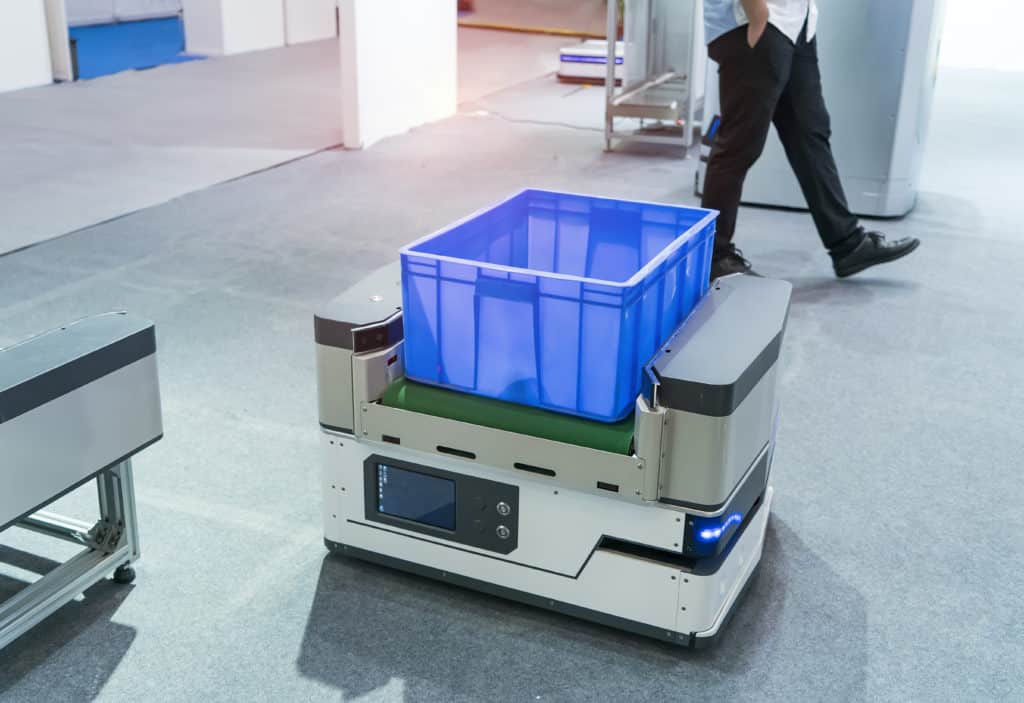
In these free path systems, a wireless access point (WAP) on a local area network (LAN) is essential. The WAP, or hotspot, allows wireless-capable devices such as AGV-mounted antennas to connect to the wireless LAN (WLAN) using WiFi or one of the IEEE 802.11 protocols. As an AGV travels through the warehouse, its antenna transmits and receives signals. Radio frequency identification (RFID) tags on warehoused products and materials also use wireless communications to support greater efficiency.
AGV Antenna Challenges
Wireless AGV antennas that rely upon line-of-sight communications (LOS) face numerous challenges. To maximize warehouse space, inventory may be tightly-spaced and stacked to the ceiling on metal shelving. The cranes and VLMs used in automated storage and retrieval systems pose additional obstructions. In factories, machinery and equipment can impede LOS communications. An AGV can only perform well when the signal is continuous, and coverage is incomplete where there are “dead spots”.
Warehouses with significant square footage may need multi-WAP systems to provide coverage for the entire area. As AGVs speed through the facility, however, communication paths may change frequently as handovers from one WAP to another occur. If there are lag times in communication, AGV movement may slow or stop altogether. Echo, noise, and channel sharing can also cause data losses. Additionally, communication between AGVs and the controller require low latencies for real-time coordination.
Smart Antenna Technologies
Smart radio and antenna technologies like MIMO can help but won’t solve AGV antenna challenges. MIMO (multiple input, multiple output) is a technology that uses multipath propagation to send and receive more than one data signal simultaneously over the same radio channel. The dominant signal is usually the LOS signal, which follows the direct path from the receiver to the transmitter. Reflected signals also arrive at the receiver, but significant variations in the received signal may occur.
MIMO enables a variety of signal paths to carry the data but is not immune from problems (such as fading) associated with multipath wave propagation. SISO (single input, single output) antennas and other forms of smart antenna technology like MISO (multiple input, single output) and SIMO (single input, multiple output) are also subject to multipath. With the numerous obstructions in warehouses and other environments where AGVs are used, a non-line-of-sight solution (NLOS) is needed.
Multi-Polarized Antennas: The Smarter Solution
AGV antennas from MP Antenna are multi-polarized for NLOS communications. They feature a three-dimensional element design and are ideal for mitigating multi-path issues in MIMO and SISO. Compared to standard antennas with similar or higher laboratory gains, MP’s products provide superior performance in obstructed environments. MP Antenna’s patented designs also outperform all other NLOS antennas in quality and reliability while providing AGV operators with faster data speeds and greater coverage.
For AGV operators, it’s important to understand that radio propagation in a highly reflective environment can be visualized as a smoke bomb that penetrates differently-shaped nooks and crannies with a variety of polarizations. At both ends of the connection, multi-polarized antennas connect more clients at higher data-throughput rates both at a distance and in closer proximity. That’s true for both non-LOS for near-LOS locations keeping AGV’s connected and operating efficiently in any application.